Q&A with Noel Greis: The Future of the Machine Tool Industry
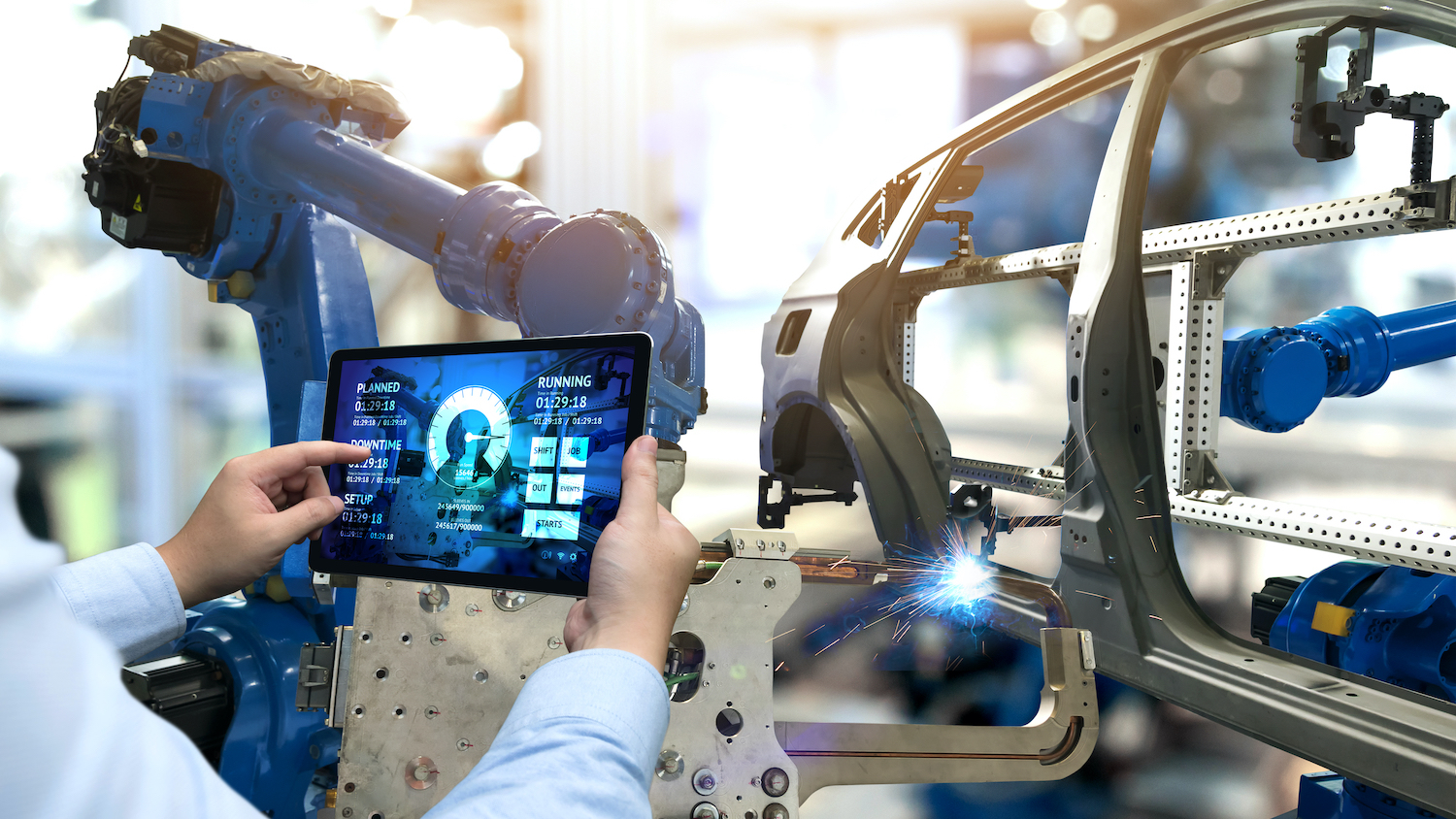
Noel Greis, research professor of operations and supply chain management in the Poole College of Management, recently received a grant from the National Science Foundation to examine critical gaps in knowledge and capacity in the U.S. machine tool industry. Over the next five years of the grant period, she will join an elite group of national thought leaders in an unprecedented push to help make the industry more competitive on a global scale.
Can you give us an overview of the machine tool industry?
Today’s products are complex assemblies of parts and components whose production typically involves specialized machine tools. These tools require a massive investment of capital to manufacture. For example, it takes billions of dollars of investment in automated fabs and specialized technology to produce silicon wafers that are used in microprocessors for cars, computers and other advanced products. Beyond the financial investment, building specialized machine tools takes specific knowledge and capabilities that can take years for companies to develop.
How does your expertise relate to machine tool manufacturing?
I actually grew up in the business. My family owns a machine tool company that produces high-precision machine tools for the aerospace and automotive industries. It was a natural fit for me to get a Ph.D. in engineering and straddle the line between tech, business and engineering at organizations like Bell Laboratories. Prior to joining the faculty at NC State, I spent 30 years at the University of North Carolina at Chapel Hill, where I researched the impact of machine learning, artificial intelligence and other digital technologies on manufacturing processes and supply chain operations.
At NC State, I co-direct the Digital Solutions Lab that is focused on these innovations. In a relatively short amount of time, we are witnessing the complete transformation of traditional manufacturing into cyber-physical systems where the fusion of machines and software creates connectivity among machines, and even among humans, on the shop floor. It’s an exciting space to research.
What makes machine tools particularly important to the future of manufacturing?
No country can be a leader in global manufacturing without a strong machine tool industry to support aerospace, automotive, defense, energy, biomedical and other critical sectors of the economy.
No country can be a leader in global manufacturing without a strong machine tool industry to support aerospace, automotive, defense, energy, biomedical and other critical sectors of the economy. The challenge is to produce traditional machine tools that are precise, flexible, affordable and intelligent. To meet the demands of the evolving manufacturing industry, the next generation of machine tools must be equipped with software and controllers that provide digital connectivity in a variety of ways, such as assessing their own state of health, making decisions about how to accomplish tasks and communicating with other machine tools on the shop floor.
How globally competitive is the U.S. machine tool industry?
The U.S. used to be the world leader in machine tools and manufacturing. Increasingly, the U.S. and other leaders like Germany are facing intense global competition. China has identified precision machine tools as one of the top 10 areas to dominate by 2025. Its government is investing heavily in the industry to close the gap in high-precision manufacturing. Chinese manufacturers are not producing products of the same quality, but they’re closing in on us, and they can innovate more cheaply with all the capital their government is providing.
The pandemic revealed how much the lack of domestic advanced manufacturing capability jeopardizes economic and national security as well as public health and safety.
The pandemic revealed how much the lack of domestic advanced manufacturing capability jeopardizes economic and national security as well as public health and safety. There was already a conversation taking place about which supply chains were critical to bring back to the U.S. after they had been offshored, and the pandemic brought that conversation to the forefront.
What is the purpose of the grant you recently received under the NSF’s Future Manufacturing program?
The grant is focused on understanding critical gaps in knowledge and capabilities that we need to develop as a nation to remain competitive. It’s an opportunity to take inventory of where we are and align our research priorities with the future we envision in the next 10 to 20 years. The Biden administration is focusing heavily on investing in U.S. manufacturing capabilities, and that investment can’t succeed without taking into account the role of the machine tool industry.
What are the intended outcomes?
In June, the research team will host a road mapping exercise in collaboration with the National Center for Defense Manufacturing and Machining (NCMDD). I’m a member of the leadership committee led by Professor Steve Schmid at UNC Charlotte that will convene about 60 leaders in academic, government and business roles to brainstorm and exchange ideas in an iterative process. After this event, we will produce a report that will make recommendations for prioritization and funding of critical research. We will also attend international trade show events to gain direct access to business leaders who are vital to industry transformation. Ultimately, our objective is to identify gaps in knowledge that must be addressed to achieve vital U.S. manufacturing goals over the next five years. If we can achieve a critical mass of thought leadership, we can do the work of accelerating the next generation of machining for advanced manufacturing.
This post was originally published in Poole Thought Leadership.